Instalacja katalitycznego odazotowania spalin w kontekście bezpieczeństwa wybuchowego
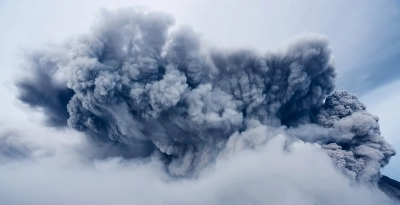
Problem wpływu działalności człowieka na środowisko oraz emisji przemysłowych zanieczyszczeń, które były wynikiem działalności nastawionej wyłącznie na zysk, pojawił się stosunkowo niedawno. Początek szybkiego rozwoju przemysłu został zapoczątkowany w XVIII wieku, natomiast jego apogeum przypadło na połowę XX wieku. Wtedy też zaczęto dostrzegać negatywne zmiany, jakie rozwój przemysłu poczynił w środowisku naturalnym.
Dla Polski przełomowym momentem w postrzeganiu roli państwa w procesie ochrony środowiska była zmiana ustroju politycznego i przejście z systemu gospodarki uspołecznionej na system gospodarki rynkowej, a następnie przystąpienie do Unii Europejskiej w roku 2004.
Obecnie Unia Europejska narzuca na kraje członkowskie coraz ostrzejsze normy dotyczące emisji przemysłowych. Polskie zakłady przemysłowe, aby przystosować się do nowych wymagań, musiały w ostatnich latach przejść gruntowną modernizację. Dla polskiego przemysłu i energetyki, opartych na węglu kamiennym, dostosowanie do unijnych norm emisyjnych wiąże się ze znacznymi nakładami inwestycyjnymi. Szczególną uwagę przywiązuje się obecnie do zanieczyszczeń powstających głównie w wyniku spalania paliw stałych: tlenku siarki (IV), tlenków azotu (NOx) oraz zanieczyszczeń pyłowych.
Zapisy Dyrektywy IED 2010/75/UE Parlamentu Europejskiego i Rady z dnia 24 listopada 2010 r. w sprawie emisji przemysłowych (obowiązującej w Polsce od 2016 r.) znacznie zaostrzyły normy emisji NOx. W najbliższych latach wprowadzone zostaną kolejne obostrzenia, ze względu na przyjęty 31 lipca 2017 r. przez Komisję Europejską akt wykonawczy ws. nowych standardów zaostrzających normy emisji dla dużych obiektów spalania, w tym dla elektrowni węglowych.
W związku z powyższymi regulacjami prawnymi stosowane dotychczas powszechnie w przemyśle metody pierwotne odazotowania, polegające na modyfikacji procesu spalania węgla w celu ograniczenia ilości powstających tlenków azotu, okazały się mieć niewystarczającą skuteczność. Pojawiła się konieczność wprowadzenia dodatkowych rozwiązań (metod wtórnych), które pozwolą na znacznie efektywniejsze ograniczenie emisji.
Metody wtórne, polegające na usuwaniu NOx z gazów spalinowych, są w stanie obniżyć emisję do wymaganego przez Dyrektywę IED poziomu, a nawet do poziomów znacznie niższych, co jest istotne z punktu widzenia najnowszych konkluzji BAT LCP, które od 2021 r. dodatkowo obniżą dopuszczalne limity emisji NOx. Metodą o wysokiej skuteczności jest technologia SCR (Selektywna Redukcja Katalityczna – ang. Selective Catalytic Reduction). Efektywność redukcji zanieczyszczeń metodą SCR określa się na 80–95% [1]. W tabeli 1. przedstawiono szczegółowe dane dotyczące wydajności odazotowania metodą SCR w zależności od użytego paliwa i technologii spalania.
Redukcja emisji tlenków azotu metodą SCR odbywa się za pomocą amoniaku lub mocznika jako czynnika redukującego tlenki azotu. Proces zachodzi w obecności katalizatora (najczęściej stosuje się katalizatory wanadowo-wolframowe na nośniku TiO2). Ze względu na niższy koszt zakupu w większości instalacji produkcyjnych używa się amoniaku.
W wyniku redukcji katalitycznej z użyciem amoniaku zachodzą następujące reakcje:
4NO + 4NH3 + O2 → 4N2 + 6H2O
2NO2 + 4NH3 + O2 → 3N2 + 6H2O
6NO2 + 8NH3 ↔ 7N2 + 12H2O
Tlenki azotu zostają zredukowane, a w zamian powstają gazy stanowiące obojętne składniki atmosfery: azot oraz para wodna. Nie należy jednak zapominać, że proces może prowadzić również do pojawienia się konkurencyjnych reakcji z utworzeniem produktów niepożądanych, np. podtlenku azotu. Aby tego uniknąć oraz utrzymać jak najlepszą wydajność odazotowania, należy odpowiednio dobrać warunki przebiegu procesu.
Zastosowanie technologii SCR wiąże się z dużymi nakładami inwestycyjnymi dla przedsiębiorstwa, ponieważ wymaga zabudowy reaktora z katalizatorem SCR wraz z instalacjami wspomagającymi (między innymi węzła magazynowania i dystrybucji czynnika redukującego).
Amoniak do celu odazotowania spalin w technologii SCR w większości przypadków przechowywany jest w zbiornikach w postaci wody amoniakalnej (stężenie do 25% amoniaku) lub amoniaku bezwodnego. Amoniak/woda amoniakalna przed wejściem do reaktora SCR musi zostać odparowany w parowniku z użyciem ogrzewania elektrycznego, pary lub gorącej wody. Następnie amoniak jest kierowany do systemu dysz wtryskujących go do strumienia spalin. Mieszanka jest następnie kierowana do reaktora SCR, wyposażonego w warstwy katalityczne. Katalizatory tego rodzaju pracują efektywnie w temperaturach 300–450°C.
Istnieją trzy podstawowe konfiguracje usytuowania aparatów SCR w istniejącym ciągu technologicznym:
Technologia „High Dust” – reaktor katalityczny umieszczony jest zaraz za kotłem energetycznym, trafiają do niego spaliny zanieczyszczone między innymi pyłem i tlenkami siarki.
Technologia „Low Dust” – reaktor katalityczny jest posadowiony za instalacją odpylania spalin i przed instalacją odsiarczania, trafiają do niego spaliny oczyszczone z pyłu.
Technologia „Tail End” – reaktor katalityczny znajduje się na samym końcu ciągu technologicznego, za instalacjami odpylania i odsiarczania spalin.
Już na etapie projektowym należy zwrócić szczególną uwagę na zagadnienie bezpieczeństwa wybuchowego w obrębie instalacji odazotowania spalin. Woda amoniakalna, stosowana najczęściej jako czynnik redukujący, nie posiada co prawda właściwości wybuchowych, ale amoniak, który może się wydzielać z jej roztworu, jest już znacznie bardziej niebezpieczny.
Jeszcze większe niebezpieczeństwo pojawia się w przypadku stosowania amoniaku bezwodnego, który bardzo gwałtownie wrze w normalnych warunkach atmosferycznych (temperatura wrzenia przy ciśnieniu 1013 hPa wynosi –33°C [2]), co może w efekcie prowadzić do powstania atmosfery wybuchowej (parametry palności i wybuchowości amoniaku przedstawiono w tabeli 2.).
Ponadto w przypadku gazowego amoniaku niebezpieczne są jego właściwości toksyczne, które ujawniają się już przy bardzo niskich stężeniach, dużo poniżej wartości stężenia odpowiadającego dolnej granicy wybuchowości DGW. Amoniak działa drażniąco na błony śluzowe i skórę, a jego większe stężenia w powietrzu wywołują także porażenie ośrodkowego układu nerwowego.
Ze względu na właściwości palne i wybuchowe amoniaku w stanie gazowym, przedsiębiorca planujący zastosowanie technologii SCR jest zobowiązany podjąć odpowiednie środki w celu zapewnienia bezpieczeństwa w obszarze instalacji. Na etapie projektu powinna zostać wykonana Ocena Ryzyka Wybuchu, która pozwoli oszacować zagrożenie powodowane przez czynnik redukujący oraz dokonać stosownych modyfikacji w projekcie, które pozwolą utrzymać ryzyko wybuchu na odpowiednio niskim poziomie oraz wyeliminować błędne założenia przed przystąpieniem do realizacji.
Przeprowadzenie wiarygodnej oceny ryzyka wybuchu wymaga [5]:
- oszacowania prawdopodobieństwa i czasu występowania atmosfery wybuchowej,
- oszacowania prawdopodobieństwa wystąpienia oraz uaktywnienia się źródeł zapłonu,
- oceny użytkowanych instalacji (w przypadku instalacji w fazie projektowania – planowanych do zainstalowania urządzeń) oraz substancji stosowanych w procesie,
- wzięcia pod uwagę ewentualnych skutków wybuchu,
- zaproponowania odpowiednich działań ochronnych (gdy będą wymagane).
Punktem wyjściowym do opracowania oceny ryzyka wybuchu powinna być identyfikacja potencjalnie niebezpiecznych substancji stosowanych w obrębie instalacji oraz dogłębna analiza ich właściwości. Należy zwrócić szczególną uwagę na warunki prowadzenia procesu i uwzględnić możliwe przemiany (np. zmiana stanu skupienia substancji), które mogą zajść w trakcie pracy instalacji.
W przypadku wody amoniakalnej, stosowanej powszechnie w instalacjach SCR, szczególnie niebezpieczny będzie proces odparowania amoniaku, który może stworzyć z powietrzem mieszankę wybuchową.
Następnie należy zidentyfikować obszary instalacji, w których stężenie gazowego amoniaku może osiągnąć poziom dolnej granicy wybuchowości. Szczególną uwagę należy skoncentrować na węźle magazynowania i dystrybucji wody amoniakalnej wraz ze zbiornikami magazynowymi – rozładunek i magazynowanie amoniaku wymagają podjęcia specjalnych środków bezpieczeństwa, aby ograniczyć prawdopodobieństwo wycieku i odparowania wody amoniakalnej do otoczenia.
W celu oszacowania ewentualnego zasięgu stref zagrożenia wybuchem wykonuje się obliczenia zgodnie z normą PN-EN 60079-10-1:2016: Atmosfery wybuchowe. Część 10-1: Klasyfikacja przestrzeni – Gazowe atmosfery wybuchowe [6].
W ramach tworzonego dokumentu oceniający wystosowuje również zalecenia dla projektantów instalacji, które stanowią znaczące wsparcie w zakresie zapewnienia bezpieczeństwa wybuchowego. Zalecenia dotyczą między innymi dostosowania urządzeń elektrycznych do kategorii sprzętu przewidzianego dla poszczególnych stref zagrożenia wybuchem lub przebiegu prac remontowych i naprawczych w wyznaczonych obszarach.
Błędnie przeprowadzona ocena ryzyka wybuchu lub jej brak może prowadzić do znacznego pogorszenia bezpieczeństwa użytkowania instalacji lub wręcz przeciwnie – do nadmiernego wzrostu kosztów inwestycji np. poprzez stosowanie sprzętu w wykonaniu przeciwwybuchowym w miejscach, gdzie tak naprawdę nie jest on niezbędny.
Warto zatem zwrócić szczególną uwagę na rzetelne wykonanie oceny, niosącej za sobą wymierne korzyści zarówno dla projektanta, jak i klienta, dla którego przygotowywany jest projekt.
Autorzy: Alicja Kowalik, Atex Wolff i Wspólnicy (GRUPA WOLFF)