Produkcja rozdzielnic w wykonaniu przeciwwybuchowym Ex p
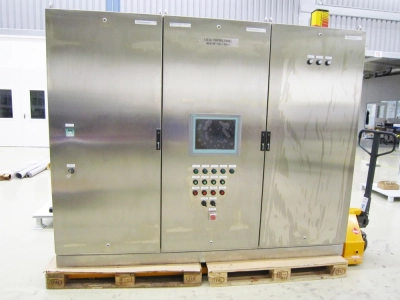
fot. Pepperl+Fuchs
Zgodnie z treścią rozporządzenia wdrażającego zapisy dyrektywy ATEX USER (1999/92/WE) pracodawca jest odpowiedzialny za ochronę zdrowia, bezpieczeństwo i odpowiedni nadzór osób pracujących w miejscu, gdzie może wystąpić atmosfera wybuchowa. Zadania te realizuje przez wydanie i wdrożenie technicznych oraz organizacyjnych środków ograniczających ryzyko powstania wybuchu, a także zapewniających ochronę przed jego możliwymi skutkami.
Stosowanie wspomnianych powyżej środków ograniczających ryzyko wybuchu powinno w pierwszej kolejności zapobiegać tworzeniu się atmosfery wybuchowej, a przy braku technicznej możliwości jej wyeliminowania, uniemożliwić zapłon atmosfery wybuchowej lub w ostateczności ograniczyć szkodliwe efekty wybuchu.
Cele te są możliwe do zrealizowania m.in. poprzez właściwy dobór urządzeń do pracy w strefach zagrożenia wybuchem. Ich odpowiedni wybór uwarunkowany jest możliwościami technicznymi zastosowanych komponentów, wielkością budżetu inwestycyjnego oraz możliwością łatwej konserwacji i naprawy (zakładamy, że niezależnie od rodzaju zastosowanej ochrony przeciwwybuchowej urządzenie zostało odpowiednio dobrane do występującego zagrożenia).
Wspomniany powyżej aspekt dotyczący obsługi jest niezwykle istotny, ponieważ urządzenia przeciwwybuchowe zachowują swój poziom bezpieczeństwa, o ile są eksploatowane w sposób prawidłowy i zgodny z zaleceniami producenta. Producent wydaje instrukcję, w której określa wszelkie dozwolone czynności w zakresie bieżącej obsługi, konserwacji i naprawy. Im bardziej utrudniona konserwacja, w szczególności dotyczy to urządzeń wymagających częstszego dozoru, tym większe mogą być zagrożenia wynikające z eksploatacji danego urządzenia w czasie.
Dobierając urządzenia do pracy w strefie zagrożenia wybuchem użytkownik ma do wyboru kilka typowych rozwiązań, których wady i zalety opisane zostały w tabeli nr 1.
Natomiast w niniejszym artykule szerzej opiszemy jedną z najbardziej wszechstronnych metod ochrony, którą jest osłona gazowa z nadciśnieniem „p”. Podstawową zasadą tego rodzaju zabezpieczenia jest zastosowanie gazu ochronnego w celu wyparcia mieszaniny wybuchowej z wnętrza obudowy i niedopuszczenia do jej ponownego wniknięcia.
Takim gazem ochronnym może być powietrze o odpowiednich parametrach jakościowych lub jakikolwiek inny gaz niepalny. Rozwiązanie to wymaga obudowy o odpowiedniej szczelności (min. IP4x lub IP3x), do wnętrza której wtłaczany jest czysty i niepalny gaz pod odpowiednim ciśnieniem. Najczęściej wykorzystuje się do tego powietrze (przy zastosowaniu sprężarki, dmuchawy czy zbiornika gazu sprężonego), dwutlenek węgla, argon, azot itp. W przypadku wykorzystania powietrza atmosferycznego jako gazu ochronnego musimy mieć pewność, że jest ono pobierane spoza obszaru, w którym mogłaby się pojawić atmosfera wybuchowa.
Przed uruchomieniem urządzenia powietrze z wnętrza obudowy powinno być usunięte i zastąpione odpowiednim gazem ochronnym (tzw. proces przewietrzania). W trakcie pracy wewnątrz obudowy powinno stale panować nadciśnienie min. 50 Pa dla wykonania „pxb” oraz „pyb” lub 25 Pa dla „pzc”. Najbardziej popularne systemy do obudów przewietrzanych bazują na stałym przepływie gazu ochronnego i jednoczesnej kompensacji ubytków w wyniku nieszczelności.
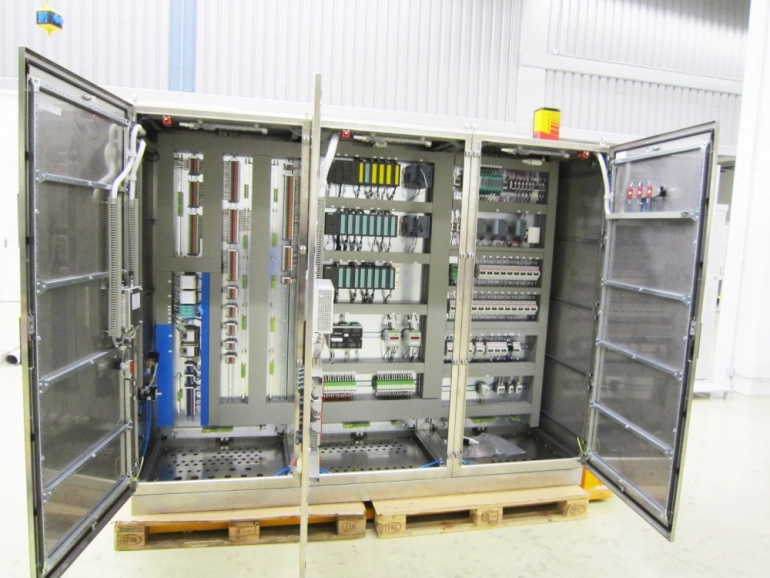
Wymagania stawiane producentom urządzeń Ex p
W przypadku produkcji urządzeń w wykonaniu Ex p mogą mieć zastosowanie następujące normy: PN-EN 60079-0 (ogólna); PN-EN 60079-2 („Ex p”); PN-EN 60079-1 („Ex d”); PN-EN 60079 -7 („Ex e”); PN EN 60079-11 („Ex i”); PN-EN 60079-15 (Ex n); PN-EN 60529 (stopień IP) oraz inne.
Od producenta urządzeń w wykonaniu Ex p oczekuje się, że posiada on niezbędną wiedzę i kompetencje, które umożliwią mu spełnienie wszystkich wymagań stawianych przez powyższe normy, o ile mają one zastosowanie. Wykonanie takich urządzeń powinno być oparte o rzeczywiste warunki panujące w miejscu końcowego montażu, przy uwzględnieniu nie tylko uwarunkowań środowiskowych, klasyfikacji stref zagrożenia wybuchem, rodzaju substancji palnej i możliwości jej emisji do wnętrza obudowy czy obecności efektywnych źródeł zapłonu, ale również o wszelkie przewidywane czynności eksploatacyjne prowadzone przez służby utrzymania ruchu czy przez operatorów danej instalacji.
Przed przystąpieniem do produkcji urządzenia z nadciśnieniem należy odpowiedzieć na następujące pytania:
- czy w obudowie znajduje się układ, który zawiera gaz lub ciecz mogące tworzyć atmosferę wybuchową (np. analizatory gazów)?
- jaki jest typ obudowy, jej rozmiar, położenie drzwi, okien oraz wszelkich innych akcesoriów, które będą montowane wewnątrz?
- jakie jest zapotrzebowanie mocy urządzeń zamontowanych wewnątrz obudowy?
W momencie podjęcia decyzji o wykorzystaniu osłony z nadciśnieniem jako środka ograniczającego zapłon atmosfery wybuchowej, należy wziąć pod uwagę szereg wymagań, opisanych w dalszej części.
W przypadku ochrony „pxb” jednostka sterująca, działająca z odpowiednim opóźnieniem czasowym, powinna odłączyć zasilanie, jeśli ciśnienie wewnątrz obudowy spadnie poniżej minimalnej, zadanej wcześniej wartości. Należy zwrócić tutaj uwagę, że takie rozwiązanie może być niekorzystne dla ciągłości prowadzonego procesu produkcyjnego i w tym konkretnym przypadku wybór osłony gazowej z nadciśnieniem „p” powinien być poddany odrębnej, niezależnej analizie. W przypadku systemów Ex „pzc” oraz „pyb” konieczne jest uruchomienie alarmu, np. sygnalizacji optyczno-akustycznej, sygnalizującej utratę ciśnienia poniżej minimalnej, bezpiecznej wartości.
Ponadto w odniesieniu do poziomu ochrony „pxb”, gdzie drzwi i pokrywy obudowy można otworzyć bez użycia narzędzi lub klucza, należy stosować blokadę, która automatycznie odcina zasilanie urządzeń elektrycznych w momencie ich otwarcia. Blokada powinna być zaprojektowana w taki sposób, aby po odłączeniu zasilania nie można było go przywrócić, dopóki drzwi nie zostaną zamknięte, obudowa odpowiednio przewietrzona (zgodnie z założeniami popartymi odpowiednimi wyliczeniami: czas i szybkość przepływu, kubatura obudowy oraz rodzaj i sposób montażu stosowanych komponentów – geometria przepływu), a nadciśnienie utrzymane dla zadanej wartości.
UWAGA: Użytkownik ponosi odpowiedzialność za sposób wykorzystywania automatycznych urządzeń bezpieczeństwa (np. w celu odłączania zasilania, uruchamiania alarmu lub zapewnienia w inny sposób bezpiecznej pracy instalacji).
Podczas prowadzonej konserwacji urządzeń przewietrzanych Ex p należy również uwzględnić niebezpieczeństwo gwałtownego otwarcia drzwi lub pokrywy na skutek nadciśnienia, w momencie, gdy zamek ryglujący zostanie odblokowany. Aby uniknąć takiej sytuacji i zapewnić bezpieczeństwo personelu, producent powinien zastosować kilka rygli w celu redukcji nadciśnienia zanim ostatni z nich zostanie odblokowany, użyć zamka dwupozycyjnego do bezpiecznego zredukowania ciśnienia, ewentualnie zredukować nadciśnienie do bezpiecznej wartości.
Kolejnym z ważnych aspektów, który należy wziąć pod uwagę, jest wytrzymałość mechaniczna obudowy i elementów łączących. Muszą one być odporne na ciśnienie równe 1,5-krotności maksymalnego nadciśnienia określonego przez producenta, panującego w warunkach normalnej pracy, nie mniejszej jednak niż 200 Pa. Jeżeli w czasie eksploatacji istnieje możliwość wystąpienia ciśnienia mogącego spowodować odkształcenie obudowy, kanałów lub elementów łączących, należy zastosować odpowiednie urządzenie zabezpieczające, w celu ograniczenia maksymalnego nadciśnienia do wartości poniżej poziomu, który mógłby niekorzystnie wpłynąć na zastosowany rodzaj zabezpieczenia.
Co ważne, właściwości materiałów stosowanych do produkcji obudowy, kanałów wentylacyjnych i elementów łączenia nie mogę ulegać pogorszeniu na skutek kontaktu z gazem ochronnym. Dodatkowo gaz ochronny nie powinien zawierać jakichkolwiek zanieczyszczeń, które mogłyby wpłynąć na skuteczność ochrony zapewnianej przez osłonę gazową z nadciśnieniem „p”. Należy również zaznaczyć, że stosowanie gazu obojętnego może stanowić niebezpieczeństwo dla personelu dokonującego bieżącej obsługi czy konserwacji urządzeń Ex p i należy w takim przypadku stosować odpowiednie środki ostrożności.
Wspominając powyżej o odpowiednich kompetencjach związanych z wykonaniem urządzeń Ex p (przede wszystkim przeznaczonych do pracy w strefie 2/22), nie należy pomijać wymagań stawianych komponentom zabudowywanym wewnątrz obudowy przewietrzanego urządzenia. Dotyczy to podzespołów zabudowanych w osobnych obudowach, których objętość jest większa niż 20 cm3. Takie urządzenia wymagają dodatkowego wewnętrznego przewietrzania, które pozwoli uniknąć jakichkolwiek obszarów (tworzących dodatkowe niezabezpieczone przedziały wewnątrz przewietrzanej obudowy), w których mogłyby gromadzić się gazy lub pary cieczy palnej.
Szczególną uwagę należy zwrócić na prawidłowe wyznaczenie klasy temperaturowej lub maksymalnej temperatury powierzchni dla produkowanego urządzenia.
W przypadku „pxb” lub „pyb” te dane weryfikowane są przez jednostkę notyfikowaną, gdzie podczas badania sprawdzana jest najwyższa temperatura zewnętrznej powierzchni obudowy oraz najwyższa temperatura wewnętrzna powierzchni stosowanych komponentów (do obliczeń bierzemy pod uwagę wyższą z nich). Z kolei dla rodzaju ochrony „pzc” to producent określa i weryfikuje wspomniane wcześniej wartości. Powinien więc dokonać pomiaru i przyjąć najwyższą wartość temperatury zewnętrznej powierzchni obudowy, biorąc pod uwagę odpowiedni współczynnik bezpieczeństwa oraz inne obecne czynniki takie jak klasa temperaturowa innych zabudowanych wewnątrz chronionej obudowy urządzeń Ex, będących pod napięciem w momencie zatrzymania przewietrzania.
Dla zachowania podwyższonego bezpieczeństwa dobrze jest również monitorować ewentualne „hotspoty” (gorące powierzchnie) przy zastosowaniu dodatkowych czujników temperatury.
Kolejną kwestią, którą należy rozważyć, jest odpowiedni sposób projektowania wlotu i wylotu gazu ochronnego. W przypadku gazów lub par cięższych od powietrza wlot gazu ochronnego powinien znajdować się blisko górnej części obudowy, a wylot w jej dolnej części. W przypadku gazów lub par lżejszych od powietrza odwrotnie – wlot gazu ochronnego powinien znajdować się w dole obudowy, a wylot w jej górnej części. Lokalizowanie wlotów i wylotów po przeciwnych stronach obudowy sprzyja wentylacji krzyżowej. Dodatkowo należy przewidzieć taki sposób montażu komponentów, który nie zakłóci przepływu gazu ochronnego.
Bardzo ważne jest również zastosowanie odpowiedniego zaworu na wylocie gazu ochronnego (łapacz iskier i cząstek stałych). Utrzymanie odpowiedniego ciśnienia w obudowie w stosunku do krzywej przepływu stanowi bowiem istotny punkt dla poprawnego przewietrzenia. Parametry te są niezależne od zastosowanego zaworu upustowego, pod warunkiem, że sam zawór spełnia wymagania co do wielkości przepływu.
Producent zaworu upustowego bada zależność między wymaganym nadciśnieniem, a krzywą przepływu i przedstawia te dane w kartach katalogowych. Jednakże, dane te, odnoszą się tylko szczelnie zamkniętej, pustej obudowy, co niestety w praktyce jest rzadko spotykane. Pojawia się więc potrzeba zastosowania odpowiedniego współczynnika korygującego dla obliczeń wielkości przepływu, po to, by utrzymać zadane ciśnienie w obudowie mimo występowania trudno mierzalnych wycieków z uszczelek, okien, aktywatorów montowanych na elewacji szafy, itp.
Dobór zaworu upustowego nie jest więc łatwą sprawą. Ten z większą szybkością przepływu może skrócić czas czyszczenia, utrzymując niskie ciśnienie w obudowie, co jest ważne w przypadku dużej kubatury. Jednakże zastosowanie takiego rozwiązania będzie wymagało częstszej kompensacji przepływu na skutek większych nieszczelności na zaworze. Z kolei zastosowanie szczelniejszych zaworów z mniejszą szybkością przepływu pozwoli zredukować ilość potrzebnego gazu ochronnego. Oczywiście nie ma ograniczeń co do wielkości obudowy przy wykorzystaniu różnych rodzajów zaworów upustowych, ale przy jego wyborze producent finalnego urządzenia powinien kierować się takimi parametrami jak: szybkość wycieku, natężenie przepływu, wymagane ciśnienie w obudowie oraz wymagany czas przewietrzania.
Innym ważnym aspektem podczas produkcji urządzeń Ex p jest odpowiedni dobór zaworu zasilającego w gaz ochronny. Na rynku są dostępne różne zintegrowane rozwiązania: zawór elektromagnetyczny do przewietrzania oraz zawór iglicowy do kontroli ciśnienia i kompensacji ubytków. Gdy jest on zasilany, zawór elektromagnetyczny jest otwarty i umożliwia wysoki przepływ gazu ochronnego. Ilość przepływu jest kontrolowana przez zawór regulacyjny. W przypadku gdy zawór nie jest zasilany, przepływ gazu ochronnego następuje przez wewnętrzny zawór iglicowy, którego nastawa wykonywana jest manualnie i wynika z wcześniejszych obliczeń bądź testów.
Należy pamiętać, że dla poziomu ochrony „pxb” producent powinien opracować odpowiednie algorytmy pracy (diagram), uwzględniające stany operacyjne urządzeń zabezpieczających i wynikających z nich działań, w tym:
- schemat przedstawiający obwód sterowania przewietrzaniem i utrzymywania nadciśnienia podczas normalnej pracy i w przypadku wyłączenia;
- schemat przedstawiający instalację przewietrzającą utrzymującą nadciśnienie, elementy składowe, mierniki ciśnienia;
- rysunek poglądowy przewietrzanej obudowy z podaniem wymiarów;
- schemat przewietrzania, montażu kanału dolotowego i wylotowego oraz sposobu ich podłączania i rozprowadzenia.
Dla poziomów ochrony „pyb” lub „pzc” zaleca się przygotowanie powyższej dokumentacji, zawierającej odpowiednią instrukcję eksploatacji obejmującą wskazówki, ostrzeżenia i zapisy dotyczące bezpieczeństwa. Instrukcja powinna być starannie przechowywana w takim miejscu, aby użytkownik urządzenia miał w każdej chwili możliwość wglądu do dokumentu.
Po stronie producenta jest również określenie warunków wymaganych do właściwego przewietrzania po otwarciu obudowy lub spadku ciśnienia poniżej wartości minimalnej. W odniesieniu do poziomu ochrony „pxb” lub poziomu ochrony „pyb” to producent określa minimalną szybkość i czas przepływu, konieczne do spełnienia wymogów normy PN-EN 60079-2.
W przypadku poziomu ochrony „pzc”, maszyn innych niż wirujące i urządzeń o złożonej geometrii, producent określa minimalny czas przepływu i czas przewietrzania potrzebne do zapewnienia przewietrzenia obudowy, jeszcze przed podaniem zasilania, gazem ochronnym o objętości 5 razy większej od objętości samej obudowy. Ilość gazu ochronnego może być zmniejszona, jeżeli skuteczne przewietrzanie zostanie potwierdzone w odrębnych, niezależnych testach. W przypadku mieszaniny pyłowo-powietrznej należy bezwzględnie usunąć zalegające na komponentach warstwy pyłu odpowiednim odkurzaczem. Przy przewietrzaniu nagromadzone pyły mogą powodować tworzenie się wewnątrz obudowy atmosfery wybuchowej (przepływ gazu ochronnego nie może powodować tworzenia się chmur pyłowo-powietrznych).
Zgodnie z powyższym standardy stosowane do oceny skuteczności „przewietrzania” (przedmuchiwania) są związane z objętością obudowy, liczbą koniecznych wymian i natężeniem przepływu przez obudowę.
Poniżej znajduje się równanie dla wyliczenia czasu „przewietrzania”:
(liczba wymiany gazu ochronnego = 5x) x (objętość obudowy) / natężenie przepływu = czas „przewietrzania”
W celu uniknięcia alarmów oraz przestojów związanych z konserwacją urządzenia przewietrzającego należy wybrać jednostkę sterującą, która posiada kompensację upływu poprzez ciągłe monitorowanie ciśnienia wewnętrznego (czujnik różnicy ciśnień) w obudowie oraz kompensację przepływu powietrza w celu uwzględnienia spadków ciśnienia poniżej wartości zdefiniowanej przez użytkownika. Jednostka sterująca powinna być zasilana z oddzielnego źródła sprzed wyłącznika głównego chronionego urządzenia.
Prefabrykowane urządzenie z układem ciśnieniowym powinno zostać ostatecznie poddane odpowiednim testom w celu sprawdzenia prawidłowości działania. Procedurę testową dla systemów Ex p należy wykonać zgodnie z normą PN-EN 60079-2. Zakłada ona między innymi (dla osłony gazowej z nadciśnieniem i kompensacją wycieków) przeprowadzenie:
- testów funkcjonalności (sprawdzenie działania urządzeń bezpieczeństwa),
- próby ciśnieniowej,
- badania natężenia przepływu gazu ochronnego podczas przewietrzania i minimalnego czasu przewietrzania,
- weryfikacji minimalnej i maksymalnej wartości nadciśnienia,
- badania szczelności przy maksymalnym ciśnieniu dla normalnych warunków pracy wraz z testem kompensacji wycieków.
Odpowiednie uszczelnienie obudowy jest istotne, by zachować minimalną wartość nadciśnienia dla danego rodzaju zabezpieczenia, która musi być wyższa niż maksymalna wartość spadku ciśnienia w warunkach normalnej pracy urządzenia, spowodowanego jego wypływem przez nieszczelności osłony.
Ważne:
pxb – urządzenia z nadciśnieniem do montażu w strefie 1 i 2 lub 21 i 22 (EPL Gb i Db); rozwiązanie to umożliwia montaż we wnętrzu obudowy wyposażenia w wykonaniu zwykłym przemysłowym
pyb – urządzenia z nadciśnieniem do montażu w strefie 1 i 2 lub 21 i 22 (EPL Gb i Db); rozwiązanie to umożliwia montaż we wnętrzu obudowy wyposażenia o poziomie EPL Gc lub Dc
pzc – urządzenia z nadciśnieniem do montażu w strefie 2 lub 22 (EPL Gc i Dc); rozwiązanie to umożliwia montaż we wnętrzu obudowy wyposażenia w wykonaniu zwykłym przemysłowym
Autor: Sebastian Słaboszewski, Dyrektor działu handlowego w GRUPIE WOLFF