Dobór pulpitów operatorskich - 6 ważnych trendów
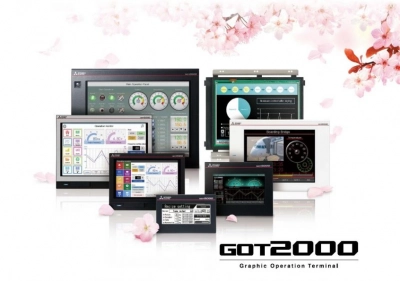
fot. Mitsubishi Electric
Jaki model wybrać, aby uzyskać wymagany poziom bezpieczeństwa, łatwość zarządzania alarmami oraz łatwość obsługi z punktu widzenia operatora?
Pulpity operatorskie zyskują coraz większe znaczenie z punktu widzenia aplikacji przemysłowych. Przestają być zwykłymi pulpitami sterowniczymi, a stają się bramami pozwalającymi operatorom na szybszą reakcję na sytuacje alarmowe. Dają podgląd na statusy poszczególnych elementów maszyny i chronią przed nieoczekiwanym dostępem. Jednocześnie interfejsy użytkownika wykorzystują ekrany o coraz wyższej rozdzielczości, pozwalając użytkownikom na dostęp do większej ilości przydatnych informacji.
Rozwój HMI pozwala zarówno operatorom jaki i zarządowi poprawę efektywności przedsiębiorstwa. Panel operatorski jest tutaj punktem wspólnym, gdzie można uzyskać więcej informacji i wykonywać więcej zadań. Czego należy oczekiwać od interfejsu HMI przy okazji kolejnej modernizacji lub zakupu nowego sprzętu?
Widoczne trendy w HMI
Należy wziąć pod uwagę sześć wymienionych niżej obszarów, w których dokonują się istotne postępy w pulpitach operatorskich
1. Większe, przejrzyste wyświetlacze
Ekrany o wysokiej rozdzielczości dają operatorom dostęp do większej liczby informacji. Łatwiej jest więc zrozumieć to, co jest wyświetlane, np. operatorzy mogą zobaczyć zmiany poziomu płynów, obserwować animacje pracy przepływomierza i uzyskać dostęp do punktów, w których zmieniając dane zobaczymy, jak te zmiany zachodzą w czasie
2. Intuicyjne alarmy
Kolejną ważną zmianą dla operatorów jest trend w kierunku intuicyjności alarmów. Ostrzeżenia te są nie tylko zaprojektowane tak, aby było je łatwo zrozumieć. Dostarczają również o wiele więcej informacji niż stosowane wcześniej światła błyskowe czy kody błędów, które często wprowadzały w błąd.
Przy wystąpieniu alarmu operatorzy mogą sprawdzić panel operatorski, aby ustalić istotność alarmu, miejsce jego wystąpienia, a nawet odszukać dokładne umiejscowienie w urządzeniu. Urządzenie może rejestrować czas wystąpienia błędu wraz z danymi poprzedzającymi wystąpienie alarmu.
Kolejny trend jeszcze bardziej ułatwi operatorom pracę. Alarmy nie tylko łatwiej zrozumieć, ale także zmniejsza się ich liczba. Wiele komunikatów będzie przesyłanych z urządzenia bezpośrednio do techników i innych osób, które muszą przeanalizować występujące problemy.
Ostrzeżenia można obecnie przekazywać inżynierom, specjalistom lub przesłać bezpośrednio do działu utrzymania ruchu, dzięki czemu operatorzy nie muszą przerywać swojej pracy, aby powiadomić dział utrzymania ruchu o każdym komunikacie alarmowym.
3. Zdolność przewidywania
Lepsze interakcje między ludźmi i urządzeniami to nie jedyny sposób rozwoju możliwości interfejsów użytkownika. Interfejsy HMI pomagają również twórcom urządzeń i użytkownikom, poprzez układy cyfrowe monitorujące parametry pracy oraz zdefiniowane algorytmy na predykcję, czyli określenie momentu, w którym elementy maszyny będą zbliżać się do awarii.
Interfejsy użytkownika pozwalają obecnie na wyświetlanie ostrzeżeń związanych ze stanem elementów urządzenia. Taka integracja pozwala pracownikom odpowiedzialnym za utrzymanie ruchu przewidzieć konieczność naprawy zamiast oczekiwania na awarię urządzenia. Dzięki tym informacjom technicy mogą dostosować harmonogramy napraw tak, aby móc wymienić elementy przed wystąpieniem awarii. Kolejną zaletą przewidywania jest możliwość lepszego zarządzania magazynem części zamiennych.
4. Łatwiejsze modernizacje starszych urządzeń
Intuicyjne alarmy można wprowadzić w formie aktualizacji oprogramowania, dzięki czemu taką funkcję można dodać do dowolnego interfejsu użytkownika. Przy założeniu, że parametry sprzętu są wystarczające, dodanie nowych funkcji do istniejącego urządzenia jest dość proste. Oprogramowanie dla pulpitu można pobrać przez sieć lub z wykorzystaniem gniazda USB. W wielu systemach gniazda USB znajdują się z przodu pulpitu operatorskiego, dzięki czemu instalacja nowego oprogramowania nie wymaga nawet od użytkownika otwierania szaf sterujących. Aktualizacje przesyłane przez sieć przemysłową są równie proste w realizacji.
5. Spójna ochrona
Interfejsy użytkownika odgrywają również rolę w cyberbezpieczeństwie, które pozostaje ważną kwestią dla szybko rosnącej liczby przedsiębiorstw przemysłowych. Coraz częściej zakłady przesyłają dane z firmowych sieci informacyjnych (IT) i sieci technologii operacyjnej (OT), które łączą wyposażenie zakładu produkcyjnego.
Często interfejsy użytkownika występują jako brama pomiędzy sieciami IT i OT. Bramy takie pomagają rozdzielać te sieci, dzięki temu problemy w jednej nie wpływają na pracę drugiej. Funkcje bramy pozwalają również przedsiębiorstwom łatwo wprowadzać rozwiązania przemysłowego Internetu Rzeczy (IIoT) na dotychczasowych lub nowych urządzeniach, przy jednoczesnym dbaniu o ich bezpieczeństwo.
6. Zintegrowane zbieranie i udostępnianie danych
Kolejną zaletą zaawansowanych interfejsów użytkownika jest fakt, że mogą upraszczać działania, zbierając dane z różnych elementów automatyki. Interfejsy użytkownika można podłączyć do wszystkich urządzeń albo tylko do głównego sterownika. Mogą one służyć jako punkt dostępu dla urządzeń pozbawionych bezpośredniego połączenia. Na przykład sterownik PLC może potrzebować informacji z urządzeń skonfigurowanych poza panelem operatorskim. O ile panel może nie mieć bezpośredniego połączenia z „niewidocznym” urządzeniem, o tyle może tunelować połączenie przez sieć i PLC, aby zapewnić dostęp do urządzeń takich jak serwo. Dzięki temu nie traci się czasu i nie ponosi się kosztów związanych ze zmianą konfiguracji urządzenia, która byłaby konieczna w innej sytuacji.
W większości systemów stacja robocza interfejsu użytkownika nie jest jedynym miejscem, w którym można zapoznać się z ostrzeżeniami. Informacje generowane przez interfejs HMI mogą być również podłączone do systemu realizacji produkcji (MES) lub za pośrednictwem inteligentnych serwerów sieciowych. Dzięki serwerom sieciowym inżynierom można prezentować bardziej szczegółowe informacje niż operatorom, co ułatwia tym pierwszym podejmowanie decyzji na podstawie większej liczby informacji jeszcze zanim dotrą do maszyny. Ostrzeżenia i raporty mogą być również automatycznie przesyłane do określonych osób, np. powiadomienie kierownika zakładu w przypadku wystąpienia problemu o poważnych konsekwencjach lub ostrzeżenie grupy ds. kontroli jakości, jeżeli pewne wartości zbliżają się do wartości granicznych.
Dzięki systemom opartym na MES dane mogą być przesyłane lub odczytywane bezpośrednio z bazy danych – każda osoba, która ma do niej dostęp, może odczytać wartości i parametry robocze dowolnego podłączonego urządzenia. Takie możliwości pozwalają kierownictwu na połączenie się z różnymi lokalizacjami i analizowanie wydajności lub zarządzanie zmianami – niezależnie od tego, czy wyszli do kawiarni czy przebywają w zakładzie firmy na innym kontynencie. Przy przechowaniu danych w systemie MES kierownictwo może monitorować dane z długich okresów, aby ustalić, które maszyny często sprawiają problemy.
Interfejsy użytkownika odgrywają rosnącą rolę w doskonaleniu wydajności
Interfejsy użytkownika nie są już wyłącznie narzędziami do nadzorowania maszyn i sterowania nimi. Wręcz przeciwnie, odgrywają kluczową rolę w różnicowaniu konkurencyjnym. Użytkownicy najnowszych technologii mają o wiele więcej możliwości niż inni, aby podejmować decyzje na podstawie szerokiego zakresu informacji, które można łatwiej analizować i stosować w praktyce, niezależnie od lokalizacji.