Co warto wiedzieć o detektorach gazu?
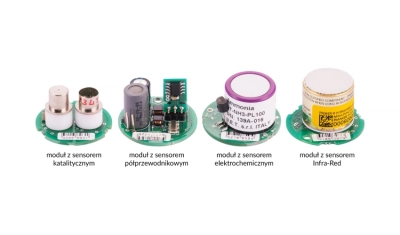
fot. Gazex
Sercem detektora gazu jest sensor gazu – element reagujący na gaz. Powszechnie, w elektronicznych detektorach gazu, stosuje się 4 rodzaje sensorów: elektrochemiczne, katalityczne, absorpcyjne w podczerwieni (Infra-Red) oraz półprzewodnikowe. W wyniku oddziaływania gazów sensory zmieniają swoje parametry elektryczne, które łatwo zmierzyć.
Sensor elektrochemiczny to rodzaj ogniwa wytwarzającego prąd elektryczny. Natężenie prądu jest proporcjonalne do stężenia gazu przenikającego do elektrolitu ogniwa. Dobierając odpowiedni elektrolit można uzyskać wysoką selektywność sensora. Nie 100%, bo może on zareagować na inne gazy o odpowiednich, zbliżonych do gazu mierzonego, właściwościach chemicznych. W trakcie pracy elektrolit się zużywa i to zużycie jest uzależnione od intensywności i czasu pracy sensora oraz stężenia gazów w jego otoczeniu. Producenci podają żywotność sensora w czystym powietrzu, a stopień jego zużycia można jedynie określić, stosując odpowiednią procedurę z użyciem mieszaniny wzorcowej gazu. Dlatego niezbędne jest dokonywanie korekt wskazań, czyli kalibracji detektorów zgodnie z ich instrukcją obsługi. Służby ratownicze wykorzystujące takie detektory, dla bezpieczeństwa, wykonują kalibrację po każdej akcji, w której wystąpiło duże stężenie gazów. Ten rodzaj sensorów wykorzystywany jest głównie do detekcji gazów toksycznych.
Działanie sensora katalitycznego oparte jest na wykorzystaniu egzotermicznej reakcji katalitycznego utleniania. Sensor zawiera element aktywny, pokryty warstwą katalizatora i bierny – bez katalizatora. Oba elementy, umieszczone w odpowiednim układzie elektronicznym, mają identyczną rezystancję w tej samej temperaturze. W przypadku pojawienia się gazu palnego reakcja utleniania następuje tylko na elemencie aktywnym. Wydzielane ciepło jest proporcjonalne do stężenia gazu i powoduje wzrost temperatury i rezystancji elementu aktywnego. W układzie pojawia się napięcie, które łatwo zmierzyć i przetworzyć na wielkość stężenia gazu. Sensor nie jest selektywny – reaguje na każdy gaz utleniający się w obecności katalizatora. Przy jego pomocy można mierzyć stężenia gazów wybuchowych do 100% dolnej granicy wybuchowości.
W sensorze Infra-Red wykorzystuje się zjawisko pochłaniania promieniowania podczerwonego przez wiązania chemiczne w cząsteczkach gazu. Różne wiązania pochłaniają promieniowanie o charakterystycznej dla siebie długości fali. Można zmierzyć stopień pochłaniania promieniowania prześwietlającego komorę pomiarową i na tej podstawie określić stężenie mierzonego gazu. Ten rodzaj sensorów najczęściej wykorzystuje się w detektorach do precyzyjnego pomiaru stężeń CO2, metanu i propanu-butanu.
W sensorze półprzewodnikowym wykorzystuje się zjawisko powierzchniowej adsorpcji gazu na elemencie pomiarowym w ściśle określonej temperaturze. Zaadsorbowany gaz powoduje zmianę rezystancji półprzewodnika, która jest powiązana ze stężeniem gazu w powietrzu. Zmiana ta jest silnie nieliniowa i z tego powodu te sensory wykorzystuje się w detektorach progowych, sygnalizujących przekroczenie określonych stężeń gazów wybuchowych lub toksycznych. Odpowiednio dobierając skład półprzewodnika i temperaturę pracy elementu pomiarowego, można uzyskać znaczną selektywność sensora. Najdoskonalszym sensorem półprzewodnikowym jest sensor tlenku węgla. Pracuje on w cyklach pomiarowych sterowanych mikroprocesorem. W zależności od rodzaju sensora taki cykl może trwać od kilku do kilkudziesięciu sekund. Dodatkowo komora pomiarowa osłonięta jest filtrem węglowym eliminującym gazy zakłócające.
Sensory nie są doskonałe, mają swoje ograniczenia. Wymagana precyzja pomiaru i warunki panujące w obiekcie determinują zastosowanie odpowiednich sensorów. Aby, budowane w oparciu o nie, detektory prawidłowo działały i spełniały oczekiwania użytkowników, muszą być właściwie dobrane. Na przykład firma Gazex do detekcji metanu wykorzystuje 8 sensorów: 5 półprzewodnikowych, 2 katalityczne, 1 Infra-Red. Równie istotna jest prawidłowa eksploatacja. Bezwzględnie należy przestrzegać terminów okresowych kontroli i kalibracji. Kalibrację mogą wykonywać tylko uprawnione osoby o odpowiednich umiejętnościach i dysponujące wymaganym sprzętem (oprogramowanie i interfejs, mieszanina kalibracyjna i zestaw dozujący gaz). Każdy sensor spełnia swoją rolę, jeżeli jest właściwie zastosowany. Jedne detektory służą do monitorowania procesu technologicznego, inne do badania stanowisk pracy, a jeszcze inne do sygnalizowania zagrożenia wybuchem czy sterowania wentylacją. Im bardziej zaawansowane technologicznie są detektory i skomplikowany jest system detekcji, tym wyższe będą koszty zakupu, montażu, obsługi i eksploatacji. Jeżeli nie ma potrzeby ciągłego, precyzyjnego pomiaru stężenia gazu i jego wizualizacji, a wystarczy system alarmowy sygnalizujący pojawienie się gazu, można poprzestać na detektorach progowych. Najczęściej takie detektory sygnalizują przekroczenie dwóch lub trzech progów. Tego typu detektory powszechnie stosuje się w budownictwie – domowe czujniki gazu, urządzenia sygnalizacyjno-odcinające w kotłowniach gazowych, detektory czadu w kotłowniach na paliwa stałe, sterowniki wentylacji w garażach, tunelach i parkingach. W tych zastosowaniach detektory reagują na stężenia co najmniej kilkakrotnie niższe niż niebezpieczne. Z powodzeniem można tu stosować detektory progowe z sensorami półprzewodnikowymi, które mają najdłuższą żywotność i długi okres między kolejnymi kalibracjami.
Wszystkie detektory firmy Gazex wyposażone są w wymienny moduł sensora. Taki moduł zawiera sensor gazu i wszystkie niezbędne elementy elektroniczne potrzebne do jego kalibracji. W przypadku konieczności kalibracji użytkownik może we własnym zakresie wymontować moduł sensora i poddać go kalibracji bądź wymienić na inny, już skalibrowany. Operacje te są przeprowadzane bez konieczności demontażu detektora z instalacji. To unikatowe rozwiązanie techniczne znakomicie ułatwia i obniża koszty eksploatacji systemów detekcji gazów. Moduły sensorów wyposażone są w procesor i zapamiętują parametry pracy sensora takie jak: ilość alarmów, czas pracy w stanach alarmowych, ilość przekroczeń zakresów pomiarowych oraz ewentualne stany awaryjne. Przy kalibracji można prześledzić, w jakich warunkach pracują detektory i, w razie potrzeby, dokonać korekt w ustawieniach parametrów pracy systemów, bądź zaproponować zmianę sensorów na inne, bardziej odpowiednie dla konkretnych warunków panujących w monitorowanym obiekcie. W przypadku zmiany technologii w zakładzie pracy i zmiany rodzajów substancji niebezpiecznych nie trzeba wymieniać systemu detekcji – wystarczy wymienić moduły sensorów na odpowiednie do zmian, co jest rozwiązaniem prostszym, szybszym i tańszym.
Aby system detekcji gazów pracował prawidłowo muszą być spełnione 4 podstawowe warunki:
- Właściwy dobór urządzeń uwzględniający warunki panujące w monitorowanym obiekcie oraz potrzeby użytkowników
Należy uwzględnić temperaturę, wilgotność, obecność gazów zakłócających pomiar, zakres pomiarowy, sposób wizualizacji i archiwizacji wyników, konieczność sterowania urządzeniami wykonawczymi, konieczność stosowania zasilania awaryjnego. Bardzo istotne jest właściwe ustalenie progów alarmowych. Powinny być na poziomie zapewniającym bezpieczeństwo – zbyt nisko ustawione mogą wywoływać niepotrzebne alarmy i mogą zakłócać funkcjonowania monitorowanego obiektu. - Właściwy wybór miejsc instalowania detektorów
Detektory wykrywają gaz w miejscu zainstalowania. Gaz musi wniknąć do komory pomiarowej. Należy wybrać miejsca najbardziej prawdopodobnego gromadzenia się gazu i powstania zagrożenia. Trzeba uwzględnić ciężar właściwy gazu, ruch powietrza w monitorowanej strefie, lokalizację otworów wywiewnych i nawiewnych. Bardzo istotne jest zapewnienie łatwego dostępu do urządzeń. - Prawidłowe wykonanie instalacji systemu
Urządzenia muszą być prawidłowo, zgodnie z instrukcją połączone przy użyciu właściwych materiałów instalacyjnych, instalacja i okablowanie winno być wykonane starannie, zgodnie z przepisami i obowiązującymi zasadami. - Prawidłowa, zgodna z instrukcją i zdrowym rozsądkiem eksploatacja systemu
Dla prawidłowego działania systemu niezbędne jest przestrzeganie zasad określonych w instrukcji obsługi. Należy bezwzględnie przestrzegać terminów kalibracji detektorów, terminów kontroli pracy systemów, terminów wymiany akumulatorów. Kontrole powinny być przeprowadzane zgodnie z instrukcją a kalibracja wykonywana przez uprawnione laboratoria w warunkach określonych przez producenta.
Źródło: gazex.pl